Succinylcholine chloride is a vital medication in anesthesia, often used to facilitate rapid muscle relaxation during surgical procedures and emergency intubations. For pharmaceutical companies involved in its production or those relying on it as part of their anesthesia product line, understanding the cost structure of succinylcholine chloride production is essential for optimizing pricing strategies and maintaining competitiveness...
Sunday, November 3, 2024

Muscimol, a naturally occurring psychoactive compound, is primarily found in Amanita muscaria mushrooms. Known for its unique neurological effects, muscimol has garnered significant interest in fields such as neuroscience, pharmacology, and alternative medicine. However, for those involved in the procurement and production of muscimol, understanding the costs associated with...
10:08 PM
Leo Frank
No comments
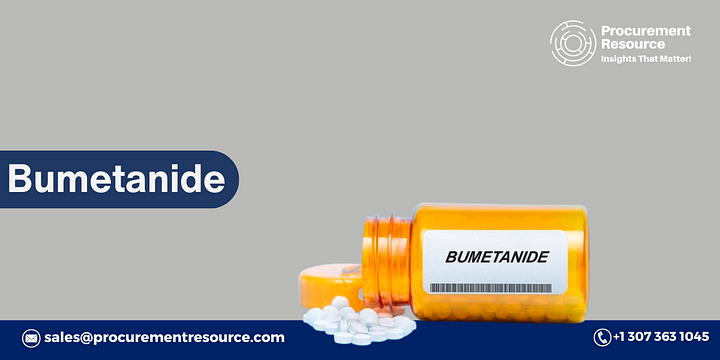
Bumetanide, a potent loop diuretic, is widely prescribed for treating fluid retention (edema) associated with congestive heart failure, liver diseases, and kidney disorders. Its efficacy in managing electrolyte and fluid balance has made it essential in medical practice. For companies involved in producing Bumetanide, understanding the cost structure is crucial. Bumetanide...
Friday, November 1, 2024
6:14 AM
Indexing Space
No comments

VP/DMAPA acrylates copolymer, a versatile ingredient used widely in the personal care and cosmetics industry, provides essential benefits as a film-forming agent and conditioning component. With its demand increasing in products like hair styling solutions and skincare, maintaining cost efficiency in its production has become crucial for manufacturers looking to stay competitive....
5:11 AM
Ben Indexing
No comments

Gallium phosphide (GaP), a semiconductor material, is highly valued for its unique properties that make it ideal for a variety of technological applications, including optoelectronic devices, LEDs, and integrated circuits. Understanding the production costs of gallium phosphide is crucial for stakeholders in industries like electronics, solar energy, and telecommunications....
3:45 AM
Ben Indexing
No comments

In today’s dynamic industrial landscape, ethyl isobutyrate is a valuable compound used across various industries, from flavor and fragrance manufacturing to pharmaceuticals and chemical synthesis. Understanding its production costs is critical for companies in these sectors, as it helps them remain competitive in an evolving market. Access to reliable, data-driven cost reports...
1:59 AM
Leo Frank
No comments

Industrial production, the Dioscin Production Cost Analysis plays a crucial role across several sectors, particularly within pharmaceuticals, nutraceuticals, and herbal medicine industries. Dioscin, a natural steroidal saponin derived from sources like Dioscorea (wild yam), is prized for its therapeutic benefits, including its anti-inflammatory, anticancer, and antiviral...
Subscribe to:
Posts (Atom)